November 24, 2017
The Source of Efficiency
In sewage water treatment, high cost pressure and an abundance of regulations put demands on owners and personnel. In water treatment plants, automation technology from Pepperl+Fuchs is used to improve efficiency.
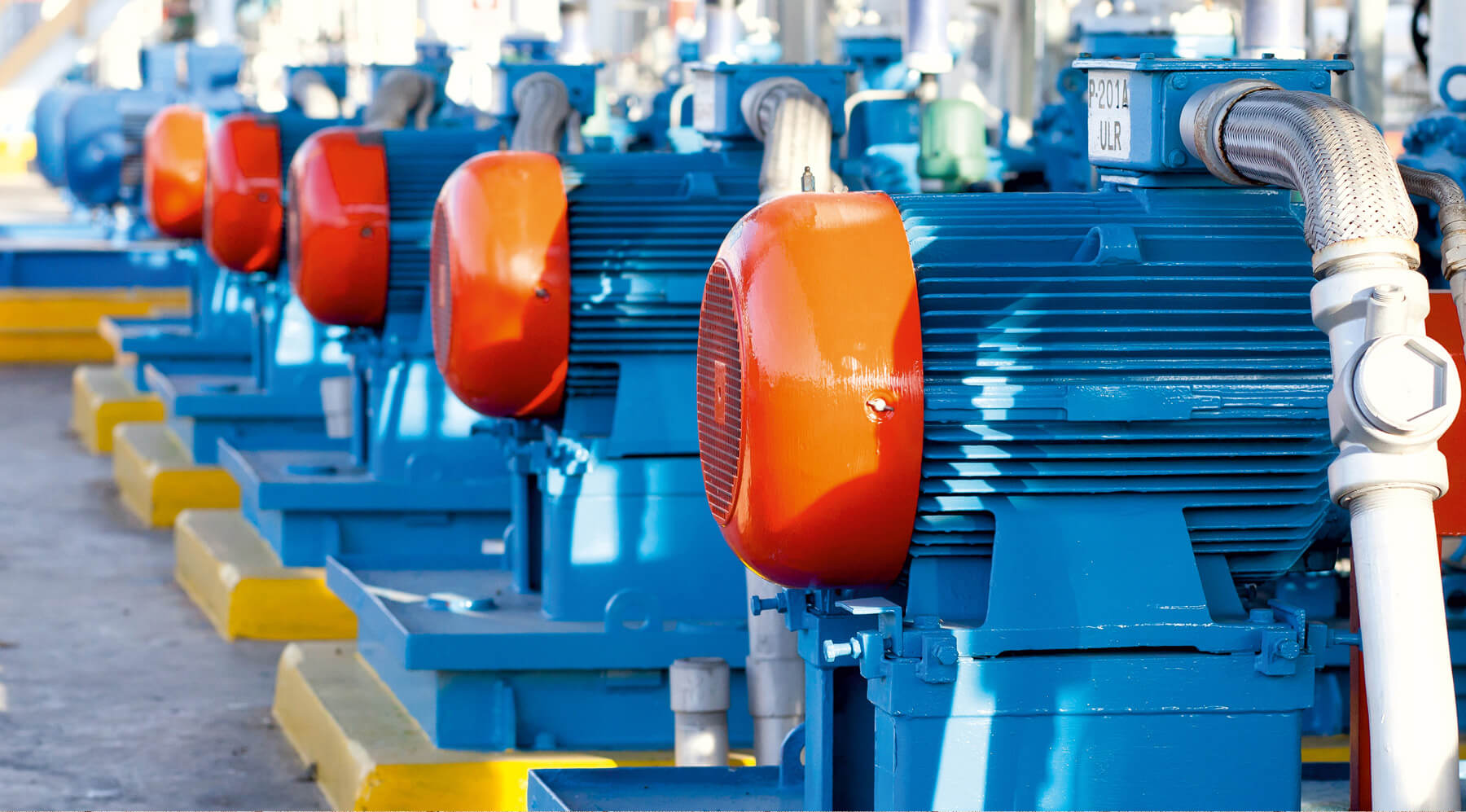
Problem Case: Pump
Oil and gas extraction in scorching hot deserts, extensive chemical plants, or wave-beaten offshore platforms—Pepperl+Fuchs solutions and products have been valued in these settings for decades. However, our expertise in explosion protection is also in demand outside of these “traditional” areas, for instance, in sewage treatment plants. High cost pressure and an abundance of regulations put demands on owners and personnel. How can a comprehensive automation solution provide relief in this difficult situation?
“Even before the sewage treatment itself, namely during the transport of water to the plant, automation technology offers great advantages because deviations and disruptions are recognized early,” says Tobias Rischer, Product Specialist in the Commercial Sales Office at Pepperl+Fuchs. “Particularly, when feed pumps are used to compensate for a lack of natural inclines. These pumps regularly have to contend with solid objects that are difficult to break down, such as wet wipes or branches,” he continues. In these cases, a frequency converter provides relief: “In cooperation with one of our binary sensors, it acts as a rotation speed monitor for the pump motor and allows for quick reaction. This ensures that a blockage of the pump does not cause complications in the plant itself,” Rischer says.
The Need for Continuous Monitoring
A maxim that applies to the entire process becomes clear at this point: an increase in efficiency depends on continuous monitoring of the various stages. In a sewage treatment plant, this is closely tied to level measurement. “Together with our expertise in various interface technologies, our portfolio of level sensors offers the basis for efficiently monitoring a sewage treatment plant. We cover an extremely wide variety of applications with hydrostatic probes, float switches, and special components such as conductive switch amplifiers and trip amplifiers,” says Business Development Manager Martin Holdefer, explaining the product lineup he manages.
At Home in Three Worlds
Pepperl+Fuchs solutions rely on both analog and digital technology for communication between the field and control level. “Whether traditional point-to-point wiring, remote I/O systems, or complete digital fieldbus infrastructure—they all have their own advantages. We work with customers to find the ideal connection of field devices for each individual sewage treatment plant. There is no standard, out-of-the-box solution,” says Rischer, explaining the customer-focused approach. For certain applications, it is important for components to be certified for use in explosion-hazardous areas. “With our decades of experience in electrical explosion protection, we are the right people to turn to when, for instance, reliable measurements need to be taken on a screening rake or an aerated sand trap,” Rischer promises.
The Fourth Dimension: HART
Another part of effective operation of sewage treatment plants is the use of HART field devices. Greater information density can be achieved throughout the entire sewage treatment process by reading out the HART variables available with these devices, thus increasing plant availability. For direct conversion of digital HART values into 4...20 mA signals—even out of explosion-hazardous areas—the HART loop converter from Pepperl+Fuchs offers a reliable solution. Additionally, the experts have also given thought to the asset management of HART field devices.
“A fully implemented HART multiplexer system allows the asset management system to communicate with up to 7,936 HART field devices. That should answer any questions about the price-to-performance ratio,” notes Andreas Grimsehl, Product Marketing Manager for Interface Technology, with a grin.
Wireless for More Flexibility
But what happens if new field devices need to be placed in a sewage treatment plant and the switch cabinets and cable trays are already packed full? “WirelessHART offers a solution in such scenarios,” says Sabrina Weiland, Product Marketing Manager for remote I/O systems and WirelessHART. “By connecting a 4...20 mA or HART-capable field device with an adapter, data can be transmitted to the control panel wirelessly.” Another common problem in sewage treatment plants can also be avoided this way. “If one of our battery-operated WirelessHART adapters is installed on the bridge of a rotating rake in the intake basin, expensive sliding contacts, which are subject to wear, are no longer necessary. The principle can also be applied to other moving system components,” Weiland demonstrates. Thanks to the adapters or temperature converters, data can also be transmitted from difficult-to-reach areas such as the digestion tower, since they can be mounted at a distance of up to 250 m.
Sewage Sludge as an Energy Source
The methane generated in this digestion tower is a key factor in energy efficiency and is more than just a waste product: in modern sewage treatment plants, combined heat and power units burn the gas obtained from sewage sludge and then use the resulting energy to operate the sewage treatment plant. Various kinds of data are required for this process, including temperature, fill level, pressure, and gas quality. To connect the necessary measuring instruments to the control system in a conventional way, interface modules like those from the proven K-System, which consists of various components for DIN rail mounting, are recommended. This system provides users with both explosion-protected and non-explosion-protected components from a single product family. As a result, operation is always the same, saving valuable time during commissioning and maintenance.
“Our products follow the water through the entire process—from the delivery of the sewage to the conversion of the sewage sludge into energy. This is only possible as a result of the pervasiveness of our solutions across different technologies,” Rischer summarizes. Real-world applications prove his point: even the containers where sludge is held prior to incineration contain Pepperl+Fuchs ultrasonic sensors for monitoring the fill level.